Una historia de los motores de aeromodelismo cordobeses
Ha ido pasando el tiempo y como es natural el paulatino asedio del olvido nos va alejando de los logros acaecidos años atrás pero que aún quedan en el recuerdo de quienes los produjeron.- Por eso nos pareció justo y valioso recordar aquella epopeya realizado por nuestro socio, el Ingeniero Juan Carlos Boccamazzo, con la invalorable contribución de Osvaldo Livi y Hugo Gutiérrez, quienes lograron hacer realidad la quimérica idea de producir motores para el aeromodelismo argentino.-
Seguramente el lector se va a asombrar de la increíble creatividad y coraje del productor y sus colaboradores.-
Ahí va el relato del autor:
Motores Boccamazzo
Siempre fui desde chico un amante del aeromodelismo y sobre todo de los motores a explosión que en él se usan-.Como estos motores eran bastante onerosos para mí, años después, comienzo de la década de los 80, se me dio la idea de fabricarlos.-A esa altura ya tenía los conocimientos necesarios para concretar mis sueños, ya que mi profesión, ingeniero mecánico-electricista, y mi ambiente de trabajo me lo permitían.
Lo primero a resolver era la fabricación de la Glow Plug, ya que se conseguían pocas importadas y bastante caras. Después de mucho invertir y probar llegué a una “bujía” que anduviera.-Esto ocurría hace unos 35 años .- El siguiente paso era hacer el motor, que encaramos junto con mi gran amigo Hugo Gutiérrez y con la gran colaboración de Osvaldo Livi, que nos fundía el cárter, llegamos a fabricar un motor .15 con válvula rotativa trasera para uso en la categoría Vuelo Libre FAI.-El motor andaba bien, pero el costo era alto y pocos los que practicaban esa categoría por lo que decidimos abandonarlo.-Ese motor lo denominamos BLG .15.
Después de este error comercial, me dispuse hacer un motor económico, utilizando el pistón del BLG, ahora la coquilla para fundir el cárter era metálica y los noyos también. Era un quince muy barato denominado RP11, no pasaba las 11000 rpm, pero tuvo un gran éxito comercial; era muy conocido entre los amigos, cariñosamente como “el bofe”.
Al tiempo, con Gutiérrez decidimos emprender la fabricación de un .20 para uso de radio con el carburador para para tal fin, lo llamamos BG20.- Lo hicimos en una versión con cojinetes a bolas y otra con buje.-Los dos nos dieron un gran resultado, tan es así que hay aún hoy algunos que andan muy bien; hicimos una cantidad interesante y se vendía bien.-Cuando decidimos ampliar la fabricación, un cambio económico, como los hay, los hubo y los habrá, dio por tierra con todos nuestros sueños.
DESARROLLO DE LA GLOW PLUG
Para seguir con el tema, me voy a seguir refiriendo a la solución de la glow.-Primeramente diseñé el cuerpo metálico y el centro, lo que siguió fue bastante oneroso ya que como eran hechos en torno automático, tuve que encargar unas 500 piezas, corriendo el riesgo de que no fueran exitosas, paralelo a esto estaban los problemas del cierre y de la junta correspondiente al mismo ya que además de ser hermética debía ser aislante eléctrica, y del consabido corazón de la glow, que era el filamento. Para el primer problema opté por lo que era más fácil conseguir, que era amianto que en forma de arandela y con otra de aluminio, conseguí un cierre eficiente.-En esos tiempos no se divulgaba el elemento con que estaba compuesto el filamento, comencé probando con alambre comercial de nicrom (aleación de cromo y níquel) del que se usa en los calentadores eléctricos, duró una explosión.-Me decidí no perder tiempo y apelé al platino y con los años, debido a la mayor exigencia, también opté por la aleación platino-rodio al 10%,este último con un punto de fusión más alto, le daba más rigidez al alambre.-Estas aleaciones no son comerciales y hay que hacerlas, yo compré el material (el rodio viene en polvo, cerca de 2000 grados su fusión) y un aeromodelista mecánico dental me fundió el platino y le agregamos el rodio.
Luego vino la historia del laminado y trefilado a un diámetro de 0,2mm,las trefilas las hice hacer de vidia y la reducción de diámetro se complicaba después de los 0,3mm,es decir que para que no se rompiera al trefilar había que reducir pocas centésimas por pasada. Bueno todo este sacrificio tuvo un buen fruto y las glow anduvieron bien. Produje alrededor de unas 3500, todavía dispongo de ellas.
Después hubo que entrar a pensar en fabricar el motor.-
Pero antes me quiero referir a algo que faltaba de las glow, esto es la soldadura del filamento. No soy de Cáncer, pero he aprendido a ser persistente, sino no hubiera aprobado Geometría Descriptiva con nueve y no fue diez porque el profe me hizo trampa.-
Pensando un poquito, me dí cuenta que lo único que podía usar era soldadura por punto, luego de encontrar un señor que hacía transformadores y explicarle mi problema, me hizo un transformador de 220V a 3V,el primario con unas 75 vueltas y el secundario con 1 vuelta, el resto del trabajo quedaba para mí.-El secundario que es la punta soldante salía con un cable de Cu de unos 6mm de diámetro y tenía soldado en el extremo un alambrito ,del mismo material, de un diámetro similar al interior del espiral del filamento.-Del rollito de alambre de platino, sin cortarlo, en su punta, hacía un espiral de cuatro vueltas, luego le introducía el electrodo y soldaba en el fondo, luego fuera, en el costado, quedaba lista.- Me olvidaba de decir que primero había armado la glow, poniendo la pieza superior con las arandelas de amianto y con un golpe cerraba la parte plegable del cuerpo exterior.-En el croquis, si bien algo desprolijo, seguramente ayudará a entender.-
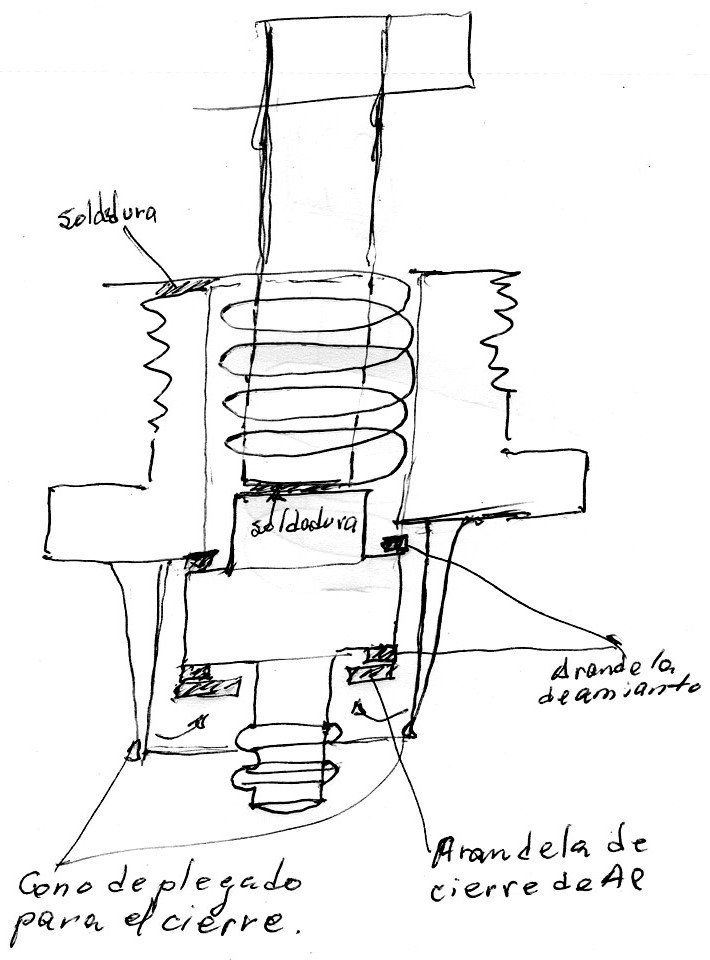
PRIMER MOTOR – BLG .15
Después de la glow, siguió la historia del primer motor, era un .15 es decir 2,5cc con pretensiones de superioridad.- Hugo Gutierrez, de una habilidad manual sorprendente, hizo el modelo en aluminio que después de cortado en dos mitades, las que fueron colocadas en placas para hacer las cáscaras de arena con resina (shell molding), simultáneamente hizo los moldes para hacer los noyos.-Todo este conjunto armado por Osvaldo Livi lo usaba para fundir el motor en aluminio.-Livi disponía de una fundición de aleaciones livianas en B°San Martín.-Luego en nuestro taller lo usinábamos, hacíamos el carburador que no era de barra pasante sino de alimentación periférica (similar, entre ellos al Rossi).-La alimentación era por el carter(trasera) lo que obligaba hacer una válvula rotativa movida por el cigüeñal, bastante complicada.-
La camisa era elaborada en acero y luego cianurada y templada; pistón de fundición gris rectificado y biela de duralumunio.-El barrido era tipo Schnuerle, con tres lumbreras de entrada en la camisa y una de escape.-La camisa luego de endurecida se las bruñía ajustándola al pistón una a una, se conseguía hacer este bruñido con una conicidad tal que entrara justo el pistón y se endureciera arriba; esto aseguraba un buen asentamiento y sin pérdidas de compresión.
El motor funcionó muy bien de entrada, conseguía las revoluciones pensadas; ahora hacía falta probarlo en un modelo con un aeromodelista ducho en la categoría Vuelo Libre FAI.-No lo conseguimos, fue nuestro gran problema, mucho más difícil que hacer el motor.-Hicimos una serie pequeña que la vendimos, creo que fue más por admiración y curiosidad que para darle uso.-Ahí quedó el sueño del motor BLG.15.-
SEGUNDO MOTOR – RP11
Como no me rendí, seguí solo tratando de corregir errores comerciales y darle a la gente algo bastante más accesible.-Hice un motor con dos escapes laterales, lumbreras rectas (muy simples de hacer),el carburador fundido con el motor y barra pasante.-Vendí muchísimos, saqué un propaganda en la revista Lupin, muy efectiva.-Al dibujo del motor lo hice a mano alzada.-Como daba 11.000 rpm, lo llamé RP11.-Se usaba mucho en U-control.-
TERCER MOTOR—BG20
Pero la idea de algo más refinado y de varios usos daba vuelta en la cabeza, para eso nos juntamos con el Hugo nuevamente y decidimos hacer un .20 para vuelo deportivo, con carburador para radio, no de mucha cilindrada, pero que entregara potencia a partir de todos los adelantos técnicos que se conocían en ese tiempo.-Lo que sucedía era que los motores de uso deportivo eran de barrido cruzado y únicamente los de competición eran barrido Schnuerle.-Para dimensionarlo, tomamos como base los mejores motores de esa cilindrada y modificamos lo que creímos necesario.-Se hizo una matriz de hierro compuesta por dos bloques electroerosionados con cada mitad del bloc, el modelo en cobre para hacer el trabajo lo hizo magníficamente Huguito, los noyos serían de arena fenolada e iban a “dibujar” dentro del bloc las cuatro lumbreras, las tres de admisión y una de escape, barrido Schnuerle.
Hicimos las pruebas de fundición y salieron muy bien. Para ofrecer algo deportivo, más barato, decidimos producir un motor con cigüeñal montado sobre buje y otro sobre cojinetes a bolas. El cuerpo del carburador era de plástico, algo complicado pero funcionaba bien.-Como siempre usamos camisa en acero cianurado y pistón de fundición gris, esta con gran característica autolubricante por el gran contenido de grafito, el perno pistón era un rodillo de cojinete.-Las pruebas nos dejaron más que satisfechos ya que a igualdad de hélice superábamos con creces (arriba de dos mil rpm) a los extranjeros de similar cilindrada, lo que después fue comprobado por el uso, con un rendimiento de 14000 RPM.-En ese tiempo se corrían carreras de autitos controlados con motores de esa categoría, y por pedido de algunos amigos, hicimos varios de prueba.- La verdad es que competíamos de igual a igual, pero surgió un problema: se partían los pistones a la altura del agujero del perno-.La rotura se debía a que el uso en auto era de aceleraciones muy bruscas y un movimiento más “rígido” ya que la hélice en aire patina, y las ruedas considerablemente menos.-Era un problema de inercia, como la fuerza es el producto de la masa por la aceleración, debíamos reducir la masa del pistón usando un material más liviano; el indicado era el duraluminio, pero que tiene un coeficiente de dilatación más elevado que la fundición, lo que tendería a engranarse en la camisa de acero.-Para resolverlo tuvimos que hacer lo mismo que hacían los extranjeros, camisa de bronce cromada y rectificada internamente.-Solucionado el problema pudimos proveer motores competitivos en el automodelismo que llegaban a 22000 RPM.-Por supuesto, tuvimos que resolver gran cantidad de detalles que sería inútil enumerar.- También creamos de uso marino.
Hicimos bastantes motores, alrededor de 20 mensuales, con un total aproximado de 300 unidades, que se vendían como el pan; y otra vez más las idas y venidas económicas y la acción de la competencia extranjera nos hicieron cejar del emprendimiento, justo cuando estábamos dispuestos a invertir para aumentar la producción.-
Juan Carlos Boccamazzo
Abril 2017
Comentarios Cerrados